Dépôt ferroviaire (locomotives à vapeur)
Un Bahnbetriebswerk , également pour le court Betriebswerk (abrégé Bw ou BW ), est responsable de la maintenance des locomotives utilisées dans le trafic ferroviaire . Surtout à l'ère des locomotives à vapeur, il était d'une grande importance pour le bon déroulement des opérations. Bw disposait d'un grand nombre de systèmes pour pouvoir effectuer ces tâches de maintenance. Le Bw avait donc besoin de beaucoup de personnel - c'était pour la plupart l'un des plus gros employeurs de la région. Si les locomotives étaient utilisées à une plus grande distance du dépôt, cela se faisait dans une locomotive attachée au BwStation de locomotive .
L'histoire et l'importance actuelle de ces installations sont présentées dans l'article Bahnbetriebswerk .
Tâches
Équipement Debout
Avant qu'une locomotive à vapeur ne soit autorisée sur la ligne , le personnel de la locomotive a dû faire beaucoup de travail préparatoire. Lors du début de service prévu, le personnel de la locomotive - le conducteur du moteur et le chauffeur - faisait rapport à la direction de la locomotive du dépôt concerné. Là, ils ont reçu les clés de leur locomotive, un livre de réparation, un itinéraire et un horaire, et une liste des limites de vitesse . Après avoir accompli toutes les formalités, le conducteur du moteur et le chauffeur se sont rendus à leur locomotive à vapeur, qui était soit garée dans le hangar des locomotives, soit sur une voie ouverte. Après avoir grimpé dans la cabine du conducteur, le conducteur a commencé par les vérifications les plus importantes: contrôle du régulateur, étanchéité des soupapes, indicateurs de niveau d'eau et test des freins. Le chauffeur a vérifié l'équipement ainsi que les réserves de carburant. Ce n'est qu'après que ces contrôles ont été effectués que le personnel a commencé sa véritable tâche.
Le chauffeur a commencé à chauffer la locomotive, puis la locomotive à vapeur s'est rendue dans une fosse d'enquête. Pendant que le conducteur du moteur regardait sous la locomotive et recherchait des dommages, le chauffeur - équipé d'un bidon d'huile et d'une seringue d'huile - devait alimenter tous les points de lubrification de la locomotive (voir photo).
Une fois tous les contrôles effectués et la pression de fonctionnement de la chaudière atteinte, la locomotive a pu sortir du hangar et se diriger vers la plaque tournante. Après que la boîte de signalisation ait dégagé les voies , la locomotive est officiellement entrée en service et est partie sur la ligne.
Désarmer
Sur les derniers kilomètres jusqu'au terminus, le chauffeur a commencé à désarmer le feu en le laissant lentement brûler en fonction des exigences de l'itinéraire. Après l'arrivée du train à la gare d' arrivée ou à la fin prévue de l'itinéraire de la locomotive, le chauffeur a éteint le chauffage à vapeur des trains de voyageurs et la locomotive a été découplée du train et s'est rendue au dépôt. Là, les stocks de charbon ont d'abord été reconstitués dans l' usine de charbon ; il y avait des bunkers correspondants pour les machines avec du pétrole et de la poussière de charbon tirant dans le Bw-s qui abritait ou fournissait de telles machines. Ensuite , la machine met à un laitier fosse , où la chaudière a été brassages sur par les travailleurs en enlevant les résidus de combustion ( de cendres et de scories ) à partir de la boîte à feu , les éteindre dans le puits et en les stockant temporairement. La décharge était un travail assez sale. Une fois le drainage terminé, nous sommes allés à la grue à eau , où les réserves d'eau ont été reconstituées. La station suivante était le système de ponçage pour le réapprovisionnement en sable de frein , qui était fait à la main dans des ateliers plus petits - à l'aide d'échelles et de seaux - sur le dôme de sable au sommet de la chaudière .
Une fois la locomotive prête pour la prochaine utilisation, elle a été soit garée dans le hangar à locomotives, soit sur une voie ouverte et nettoyée par le chauffeur. Les réparations ont été effectuées par le personnel responsable pendant la période de repos. Les machines qui étaient censées être réutilisées à brève échéance étaient maintenues au chaud, pour lesquelles un radiateur de hangar dans la chambre de combustion maintenait un feu silencieux.

Laver
La chaudière d'une locomotive à vapeur devait être nettoyée des résidus d'évaporation à intervalles réguliers. Cela s'est produit dans le dépôt à des dates précises. La distance entre les deux dates était déterminée par la qualité de l' eau d'alimentation de la chaudière , la fréquence d'utilisation et le stress exercé sur la locomotive par rapport aux itinéraires qu'elle parcourait. Le lavage d'une locomotive à vapeur comprenait six étapes de travail:
D'abord la vapeur et une fois la bouilloire refroidie, l'eau de la bouilloire a dû être vidangée. Après cela, le nettoyage de la chaudière pouvait commencer, par lequel les dépôts de calcaire sur le fond de la chaudière et les boues étaient rincés dans des dispositifs de collecte des boues à travers des trappes de lavage spéciales à l'extérieur de la paroi de la chaudière avec un jet d'eau net. La bouilloire sur pied a ensuite été lavée de haut en bas. Si nécessaire, les dépôts de calcium excessifs devaient être éliminés. Ensuite, la chaudière a été remplie et chauffée à nouveau.
Lors de la dernière course de la locomotive avant le nettoyage prévu, les préparatifs du lavage ont commencé.
Délai et travaux prévus
Pendant que les ouvriers de l'usine étaient occupés à laver une locomotive, les serruriers s'occupaient des délais et de la planification. Ce travail était nécessaire pour maintenir la machine opérationnelle le plus longtemps possible entre les principales inspections. Afin de réduire au maximum le temps d'arrêt de la machine, ces travaux ont été étalés sur toute l'année. Les travaux les plus importants comprenaient l'inspection semestrielle des freins, la procédure trimestrielle d'essai de stabilité et une inspection annuelle des freins principaux. D'autres travaux sont énumérés dans le tableau ci-dessous.
|
|
Trains spéciaux
En plus de l'entretien de toutes les locomotives, certains dépôts sont également responsables de l'entretien des trains de service spécial. Les unités les plus importantes sont les trains de secours ou les trains de service spécial (Suisse) (par exemple pour le rechargement des véhicules déraillés ) et les véhicules de déneigement . Il y avait également des trains d'extinction d'incendie pour éteindre le plus rapidement possible les incendies à proximité. Pour le bon fonctionnement dans un dépôt ou être remorqué locomotives de manœuvre nécessaires, les wagons et les véhicules de traction non motorisés se déplacent. Presque tous les dépôts avaient une grande variété de véhicules spéciaux.
Investissements
Installations d'exploitation
Un grand nombre de systèmes différents étaient nécessaires pour entretenir une locomotive à vapeur.
Approvisionnement en eau
En plus du charbon, de l' eau était nécessaire pour faire fonctionner les locomotives à vapeur . C'est pourquoi l'approvisionnement en eau d'un dépôt a joué un rôle important. Afin de pouvoir garantir cela, presque tous les dépôts ferroviaires disposent de leur propre réseau de distribution d'eau. Ces aqueducs étaient équipés de divers systèmes d'extraction d'eau (pompes, conduites, réservoirs d'eau et points d'extraction). Certains dépôts ferroviaires disposaient de deux installations hydrauliques différentes: une usine ferroviaire qui fournissait de l'eau utilisable pour le fonctionnement des machines et une station d'eau potable qui stockait l'eau pour les employés du dépôt. Du fait du raccordement au réseau d'eau régional, de nombreux dépôts ferroviaires ne disposent plus d'installations d'eau potable. L'eau a été prélevée dans les sources, les puits et les étangs, puis purifiée. L'eau industrielle pour le fonctionnement des locomotives à vapeur devait pouvoir atteindre un haut niveau de qualité. C'est pourquoi les usines de distribution d'eau des chemins de fer ont développé leurs propres systèmes de filtration, où l'eau était traitée pour qu'elle soit utilisable pour l'exploitation. En particulier, la teneur en sel et le degré de dureté de l'eau ont été déterminants pour la facilité d'utilisation.
Après avoir nettoyé l'eau de service, elle était pompée dans un château d'eau et y était stockée. Ces systèmes avaient des formes différentes, il n'y avait pas de conception uniforme. Tous les châteaux d'eau avaient plusieurs colonnes montantes et descentes. Les châteaux d'eau alimentaient tous les systèmes en eau utilisable, y compris les grues hydrauliques . À l'aide de ces dispositifs, les approvisionnements en eau des locomotives à vapeur ont été reconstitués ( annexe ou réservoir d'eau). Les grues hydrauliques étaient pour la plupart situées près des fosses d'enquête ou à proximité de l'usine de charbon. Il y avait aussi une grande variété de modèles, mais ceux-ci ont été progressivement remplacés par des modèles standard.
Les dépôts ferroviaires de grande et moyenne taille disposaient de leur propre laboratoire qui surveillait en permanence le traitement de l' eau , le traitement de l'eau d'alimentation des chaudières étant notamment contrôlé. Des enquêtes sur l'eau d'alimentation de la chaudière ont été menées. Le laboratoire a déterminé la teneur en sel, la valeur du pH et la composition de l'eau d'alimentation de la chaudière. Le personnel de la locomotive devait apporter des échantillons d'eau d'alimentation de la chaudière au laboratoire à intervalles réguliers. Outre les contrôles de l'eau, le laboratoire était également responsable du contrôle des huiles et graisses lubrifiantes fournies .
Hangar à moteur
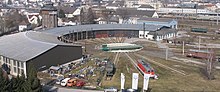
Chaque grand dépôt avait sa propre rotonde avec un plateau tournant . Les locomotives ont été mises en marche sur le plateau tournant et garées dans le hangar à locomotives. Celles-ci pourraient être chauffées, car les locomotives à vapeur n'étaient pas autorisées à se refroidir complètement, sinon le chauffage prendrait trop de temps. Pour déplacer les locomotives à vapeur à coupure froide, la plupart des locomotives retardaient les vents installés. Il était obligatoire pour presque toutes les compagnies de chemin de fer de pouvoir garer au moins 75% de toutes les locomotives dans le hangar à locomotives, le reste étant garé sur des voies ouvertes. Les grands dépôts avaient aussi souvent deux ou trois cabanes rondes avec les platines associées. Cependant, la rotonde dépendait du plateau tournant, en cas de panne, les locomotives ne pouvaient pas sortir de la remise. Le plateau tournant avait donc un entraînement de secours (à air comprimé). Au fil du temps, une conception standard d'une longueur de scène de 26 mètres a été développée. Les platines étaient toujours exposées aux intempéries et devaient être entretenues à intervalles réguliers. En fait, chaque dépôt avec une plaque tournante aurait dû avoir un triangle de voie pour que les locomotives puissent continuer à tourner en cas de défaillance des plaques tournantes, qui étaient généralement très chargées. Cependant, comme les triangles de piste nécessitaient beaucoup d'espace, ils étaient rarement trouvés. Les petits dépôts n'avaient souvent qu'un hangar rectangulaire qui pouvait être atteint à l'aide d' interrupteurs . Chaque dépôt ferroviaire devait disposer d'un terrain constructible suffisant pour pouvoir l'étendre de tous côtés. De plus petits travaux d'entretien étaient effectués dans le hangar à locomotives lui-même, pour les autres travaux de réparation et d'entretien, il y avait généralement un atelier de locomotives, qui disposait généralement également d'une grue de chargement avec laquelle les pièces de rechange lourdes pouvaient être déplacées.
Système de ponçage
Une friction statique suffisante entre la roue et le rail est nécessaire pour une exploitation ferroviaire sans problème. Les locomotives à vapeur avaient donc un ou deux conteneurs de sable sur le dessus de la chaudière, qui étaient entretenus dans les systèmes de sable. Celles-ci avaient un bunker ou une tour de ponçage et une installation de stockage pour le sable traité. Sur une tour de ponçage, un tube télescopique était verrouillé dans le bac à sable de la locomotive et celui-ci était ensuite rempli au besoin. Les dépôts disposaient généralement de sable pendant environ 30 jours.
Usine de charbon

Chaque dépôt ferroviaire avait un ou plusieurs systèmes de charbon (interdictions de charbon) qui avaient les tâches suivantes: Il était responsable de l'alimentation et du déchargement du charbon . Elle devait également stocker le carburant et faire le plein de carburant des locomotives. Les centrales au charbon étaient de types et de tailles différents, ces deux critères dépendant de la livraison quotidienne de carburant aux locomotives à vapeur. Le carburant était livré par chemin de fer, soit avec des wagons de fret normaux, soit avec des wagons spéciaux à auto-déchargement. Le charbon était stocké dans de grands bunkers à charbon, ceux-ci avaient pour la plupart des parois latérales en béton (dans le cas des dépôts plus petits, ceux-ci se composaient de vieilles traverses et de morceaux de voie ). Chaque dépôt stockait les besoins quotidiens en carburant dans un bunker principal, le charbon restant était stocké dans un ou plusieurs bunkers de réserve.
La livraison aux locomotives peut se faire de différentes manières. De nombreux dépôts ont amené le charbon du Bansen avec Hunten sur sa propre voie à une grue rotative, qui a ensuite pris la chasse et a basculé le contenu dans l'offre de la locomotive. Les grands dépôts avaient des plates-formes tombantes ou de grands systèmes de charbon qui avaient quatre bunkers remplis en forme d'entonnoir et munis d'une serrure. Si cela était enlevé, le charbon coulait dans les offres des locomotives. Dans cette variante, le charbon était alimenté aux quatre petites interdictions des interdictions principales par une grande grue. Étant donné que ces deux variantes nécessitaient beaucoup d'espace, des centrales à charbon inclinées ont été construites dans des opérations de petite et moyenne taille. Le charbon était également transporté avec Hunten, puis poussé dans une sorte d'ascenseur, tiré vers le haut puis basculé - de sorte que le charbon coulait également dans l'annexe de la locomotive à vapeur.
En plus de l'usine de charbon, il y avait souvent des grues hydrauliques et des bâtiments de service. De plus, il y avait souvent des salles de stockage à proximité de ces installations.
Usine de purification
Dans la station d'épuration, lorsqu'une locomotive à vapeur a été démontée, la grille, le bac à cendres et la chambre à fumée ont été nettoyés, car jusqu'à 20% des résidus de combustion restaient lorsque le charbon était brûlé. Ceux-ci ont été grattés avec divers outils (grattoirs, crochets et brosses spéciales) et placés dans la fosse à scories. Des fosses à scories ou des canaux de scories étaient situés à l'extérieur sur des pistes spéciales de scories. Le puisard de laitier restant après le nettoyage a été stocké dans la fosse jusqu'à ce qu'il soit vidé. Cela a été fait à la main ou avec un ascenseur incliné (voir photo à droite). Le laitier a été pelleté dans Hunte, celui-ci a été tiré vers le haut, basculé et le laitier est tombé dans un wagon avec lequel il a été transporté.
Dispositifs de soufflage
Pendant le fonctionnement, des morceaux de charbon non brûlé, des cendres et des particules de laitier se sont déposés dans les tuyaux de chauffage et de fumée, c'est pourquoi ces tuyaux ont dû être soufflés à intervalles fixes. Cette procédure avait généralement lieu après 500 à 1 000 kilomètres de marche de la machine. Le dispositif de soufflage se composait d'une plate-forme de travail mobile et d'un tuyau. De l'air comprimé a été pompé dans ce tuyau, puis tous les tuyaux de chauffage et de fumée ont été soufflés avec. Il y avait des employés pour cette activité, et ce travail a été effectué sur une piste ouverte spécifique. Le soufflage de tous les tuyaux pouvait prendre jusqu'à une heure, un 01.5 avait jusqu'à 168 tuyaux de chauffage et de fumée, par exemple.
Niveau de lavage
Les chaudières des locomotives à vapeur devaient être nettoyées à intervalles réguliers. Bien que l'eau d'alimentation de la chaudière ait été minutieusement filtrée, elle contenait des composés chimiques qui ne se sont pas complètement évaporés. Ces composés se déposent alors sous forme de boues et de tartre, ce qui pourrait conduire à un colmatage des canalisations, gêner le transfert de chaleur dans la chaudière et ainsi mettre en danger le fonctionnement de la machine. Pour cette raison, la chaudière a dû être lavée tous les 10 à 14 jours ou après 2 000 kilomètres pour les locomotives express et 1 500 pour les locomotives de fret. Le lavage à froid de la chaudière prenait jusqu'à 14 heures et le lavage à chaud nécessitait un système de lavage spécial. Pour cette opération, il y avait une voie de lavage séparée dans la remise des locomotives avec un canal de lavage, et chaque dépôt avait une autre voie de lavage à l'extérieur de la remise des locomotives. L'eau utilisée s'écoulait dans ce canal et pouvait être utilisée à d'autres fins si nécessaire.
Château d'eau du musée ferroviaire de Bochum-Dahlhausen
Grue à eau à Stützerbach
Equipement technique
En plus des systèmes d'exploitation, chaque dépôt disposait également de nombreux systèmes techniques. Celles-ci comprenaient des plates - formes de transfert et des platines , par exemple . Les éviers d'essieu étaient également très importants . Celles-ci étaient pour la plupart logées dans le hangar à moteur ou dans l'atelier. Avec ces machines, changer d'axe était relativement facile. Il y avait de nombreux designs différents, c'est pourquoi un design standard a été développé. À l'aide d'un renfoncement d'essieu, l'installation et le retrait d'un essieu pouvaient être effectués en une demi-heure seulement.
Les ateliers du dépôt ferroviaire disposaient également de leurs propres tours de roues pour les petits travaux de réparation. L'usure accrue des pneus des roues a rendu nécessaire de travailler sur le contour avant les visites programmées à l'atelier de réparation. Chaque atelier était également équipé d'une large gamme d'outils. Dans le cas des dépôts ferroviaires de taille moyenne et grande, l'atelier a été divisé en différents départements. Il y avait donc un atelier mécanique séparé , une forge , une production d'outillage , une serrurerie , une fonderie et un atelier électrique (mais cela n'avait guère de sens). En plus des départements, il y avait aussi des groupes pour des travaux spéciaux. Par exemple, nous avons créé nos propres ateliers de réparation de pompes et de chaudières.
Autres plantes
Outre les installations d'exploitation, un dépôt comprenait également des salles sociales (douches et lavabos, salons pour le personnel du dépôt et des locomotives, des couchages pour le personnel des locomotives et, dans les grands dépôts, une cantine). Étant donné qu'un dépôt avait souvent des systèmes de voies étendus, il se voyait souvent attribuer sa propre boîte de signalisation , à partir de laquelle le plan d'action était contrôlé et dirigé.
administration
Groupes de travail
Afin d'optimiser le flux de travail, des tâches individuelles ont été affectées à différents groupes de travail:
- Groupe A: questions administratives,
- Groupe B: Service de locomotive,
- Groupe C: Réparation de locomotives,
- Groupe D: service d'exploitation et réparation de wagons,
- Groupe E: systèmes mécaniques,
- Groupe F: stockage de carburant et
- Groupe K: service de véhicules.
Ce système était utilisé à la fois par la Deutsche Bundesbahn et la Deutsche Reichsbahn, la Reichsbahn avait juste des noms différents pour les groupes. L'administration fonctionnait de la même manière en Autriche, les processus de travail étaient également précisément répartis ici.
Groupe A: Questions administratives
Le groupe A n'existait généralement que dans les grands dépôts, car c'était là que l'effort administratif était le plus important. Dans le cas des petits services, le responsable du dépôt a assumé ces tâches, tandis que dans le cas des dépôts de taille moyenne, les tâches administratives ont été réparties entre les groupes B et C. Le groupe A a dû créer un aperçu de la rentabilité et un aperçu des performances des locomotives. Elle était également responsable de l'ensemble de la masse salariale (paiement des primes d'économie de carburant et paiement des vacances et des indemnités de maladie). La tenue des carnets de service et des listes de service des locomotives (y compris le kilométrage et la consommation de carburant du matériel roulant) ainsi que le suivi de la consommation d'énergie et de la consommation de matériel d'exploitation (notamment le charbon, l'eau et le gaz ) étaient également du ressort de ce groupe.
Groupe B: Service de locomotive
Le groupe B était responsable de l'exploitation des locomotives. Il était dirigé par un inspecteur, qui était généralement également le chef adjoint du service, qui était secondé par divers assistants et gestionnaires de locomotives. La tâche de créer des listes de service et des horaires de travail a ensuite été reprise par des soi-disant technologues. La plupart des grands dépôts ferroviaires avaient également un conducteur de train externe et leur propre planificateur de service. Les petits dépôts ont transféré les tâches de ce groupe au répartiteur de locomotives. Le groupe B, qui à la Deutsche Reichsbahn était désigné comme la section d'exploitation des locomotives , devait s'occuper de toutes les questions relatives aux services de locomotive et de ravitaillement. Cela comprenait également le suivi opérationnel des véhicules de traction, la clarification des dysfonctionnements et des dysfonctionnements, la création de plans de service et de circulation, l'affectation du personnel et des machines, le contrôle des carnets de service, la formation du personnel, la gestion de tous les documents et la fourniture et l'entretien de tous les véhicules de traction (chauffage, charbon, nettoyage) à leurs devoirs.
Groupe C: Réparation de locomotives
Le groupe C - réparations de locomotives - était également géré par un inspecteur de la Reichsbahn. Il s'agissait principalement du chef adjoint du service, auquel plusieurs contremaîtres étaient subordonnés en fonction de la taille du dépôt respectif. Ce groupe se composait de plusieurs colonnes de travail (un maximum de 30 employés), qui à leur tour étaient subordonnées à plusieurs contremaîtres. La Deutsche Reichsbahn a également appelé ce groupe le département de divertissement des locomotives . Le groupe C était responsable des travaux de réparation et d'entretien, de la remise du matériel roulant endommagé aux ateliers de réparation, de la commande des pièces de rechange et du matériel, y compris la gestion du magasin de pièces de rechange, le suivi des nouveaux assemblages sur les véhicules, la mise à disposition d'un train de sauvetage et la correction des pannes.
Groupe D: Service et réparation de voitures
Le groupe D jouait un rôle particulier dans les dépôts, car tous les dépôts ne disposaient pas d'un tel département. Les usines de plus petite taille attribuaient les tâches de ce groupe à un championnat distinct du groupe C, qui comptait au maximum 40 employés. Des groupes D plus importants ont été regroupés en services indépendants à la fois à la Bundesbahn et à la Reichsbahn dans les années 1950, appelés travaux de voitures de société. Si tel n'était pas le cas, le groupe D était dirigé par un inspecteur de la Reichsbahn auquel, selon la taille de l'usine, jusqu'à trois capitaines de wagons étaient subordonnés. Cette zone a été utilisée pour la vérification des rapports de dommages, la réparation des dommages et des défauts, la vérification des maîtres de wagons dans les gares, la clarification des irrégularités de fonctionnement, le remplissage des systèmes de remplissage et de désinfection de gaz pour les wagons, le nettoyage, l'éclairage et le chauffage des wagons, les travaux d'entretien et de réparation, la livraison des wagons. Responsable des ateliers de réparation, de la commande des pièces de rechange et du matériel, y compris l'administration du magasin des pièces de rechange et l'observation des nouveaux montages sur les wagons.
Groupe E: systèmes mécaniques
La composition du groupe E dépendait de la taille du dépôt respectif. Chez DR, ce groupe était appelé le département «Systèmes techniques». A la Bundesbahn, ce département a de nouveau été divisé en deux sous-groupes. Le groupe était dirigé par un inspecteur de la Reichsbahn dans des dépôts ferroviaires de taille moyenne et plus grande. Pour les petits départements, le groupe E se composait d'un maximum de 20 cheminots - ceux-ci appartenaient pour la plupart au groupe C. Ce groupe était crucial pour un bon fonctionnement. Son domaine de responsabilité comprenait l'entretien des systèmes de gaz, d'eau, de vapeur et de chauffage ainsi que les systèmes de charbon, de ponçage et de chargement (les systèmes de grue, les plateaux tournants et les plates-formes de transfert faisaient également partie de son domaine de responsabilité), l'entretien des systèmes électriques, l'entretien des balances ferroviaires et des freins de voie, Commande de pièces de rechange et de matériel comprenant l'administration du magasin de pièces de rechange et l'instruction et le contrôle des machinistes.
Groupe F: Stockage des consommables
Les plus grands dépôts avaient leur propre département qui était responsable du stockage du carburant - Groupe F. Grand livre d'équipement (une sorte d'inventaire) et stockage des matériaux d'exploitation et contrôle des employés de l'entrepôt.
Groupe K: service véhicule
Le groupe K a été formé dans les années 1930, mais il n'existait que dans quelques dépôts. Dans les années 1950, la Reichsbahn et la Bundesbahn ont séparé le groupe K et l'ont finalement converti en soi-disant dépôts de véhicules automobiles . Le groupe K était subordonné à un inspecteur de la Reichsbahn et avait pour tâches d'utiliser et d'entretenir les véhicules, de transférer les véhicules aux ateliers de réparation, de contrôler et de gérer le magasin de carburant et de contrôler les chauffeurs.
la main d'oeuvre
L'effectif d'un dépôt ferroviaire se composait d'un chef d'état-major, des agents de contrôle, des fonctionnaires de l'entreprise, des artisans, des ouvriers d'usine et des employés administratifs. Le chef d'un dépôt ferroviaire était le chef de service - il avait principalement une formation en génie mécanique et était ingénieur . Dans le cas des petits bureaux, il arrive souvent que le chauffeur le plus ancien prenne la tête. Le chef de service était responsable de la sélection du personnel et était également autorisé à organiser des examens. Il était aussi une sorte de chef de la sécurité, car il devait surveiller le respect des règles de sécurité et de travail; il était également responsable de la propreté du dépôt. Comme presque tous les chefs de service avaient une formation de conducteur de train, ils devaient aider en service lorsque le trafic était élevé. En cas d'accidents graves ou d'autres événements, le chef du service devait se présenter immédiatement.
Voir également
Littérature
- Volker Großkopf, Dirk Rohde, Markus Tiedtke: Bahnbetriebswerke Partie 1, Stations de petites locomotives . Dans: Eisenbahn-Journal Anlagenplanung 2, 2001. Verlagsgruppe Bahn GmbH, Fürstenfeldbruck 2001, ISBN 3-89610-073-4 .
- Volker Großkopf, Dirk Rohde, Markus Tiedtke: Bahnbetriebswerke. Partie 2: Stations de locomotive de taille moyenne . Dans: Eisenbahn-Journal Anlagenplanung 4, 2002. Verlagsgruppe Bahn GmbH, Fürstenfeldbruck 2002, ISBN 3-89610-102-1 .
- Peter Koehler, Wolfgang List: Das Bahnbetriebswertk pour l' ère de la locomotive à vapeur , transpress 1987 alba ISBN 3-87094-216-9
- Michael U. Kratzsch-Leichsering, Dirk Endisch: La locomotive à vapeur dans le dépôt . Transpress, Stuttgart 1999, ISBN 3-613-71096-X .
- Jan Reiners: C'est ainsi que fonctionne le dépôt . Transpress, Stuttgart 2006, ISBN 3-613-71279-2 .
- Dirk Rohde, Markus Tiedtke: Bahnbetriebswerke. Partie 3: Grandes gares de locomotives . Dans: Eisenbahn-Journal Anlagenplanung 4, 2003. Verlagsgruppe-Bahn GmbH, Fürstenfeldbruck 2003, ISBN 3-89610-116-1 .
- Dirk Rohde, Markus Tiedtke: Bahnbetriebswerke Partie 4: Groß-Bw . Dans: Eisenbahn-Journal Anlagenplanung 4, 2004. Verlagsgruppe Bahn GmbH, Fürstenfeldbruck 2004, ISBN 3-89610-129-3 .
- Markus Tiedtke: dépôt ferroviaire. Partie 1: charbon et ponçage . Dans: EK-Special 19. EK-Verlag GmbH, Freiburg.
- Markus Tiedtke: dépôt ferroviaire. Partie 2: eau sur . Dans: EK-Special 24. EK-Verlag GmbH, Freiburg.
- Markus Tiedtke: dépôt ferroviaire. Partie 3: platines et hangar moteur . Dans: EK-Special 34. EK-Verlag GmbH, Freiburg.
- Walter Weikelt, Manfred Teufel: La technologie de réparation des locomotives à vapeur . Transpress, Stuttgart 2005, ISBN 3-613-71256-3 (réimpression de l'édition de Berlin 1962).
Notes de bas de page
- ↑ Voici comment fonctionne le dépôt , pp. 142–148.
- ^ Conducteur de train de profession , pp. 57–71.
- ↑ Voici comment fonctionne le dépôt , pp. 149–152.
- ↑ C'est ainsi que fonctionne le dépôt , pp. 152–156.
- ↑ Voici comment fonctionne le dépôt , p. 156.
- ↑ Voici comment fonctionne le dépôt , p. 153.
- ↑ Comment fonctionne le dépôt , pp. 126–139.
- ↑ Modellbahnreport 73, Der Kohlen-Elevator , 2005, p. 16.
- ↑ Modelleisenbahner , numéro 6, juin 2006, pp. 18–23
- ↑ Voici comment fonctionne le dépôt , p. 14-18.